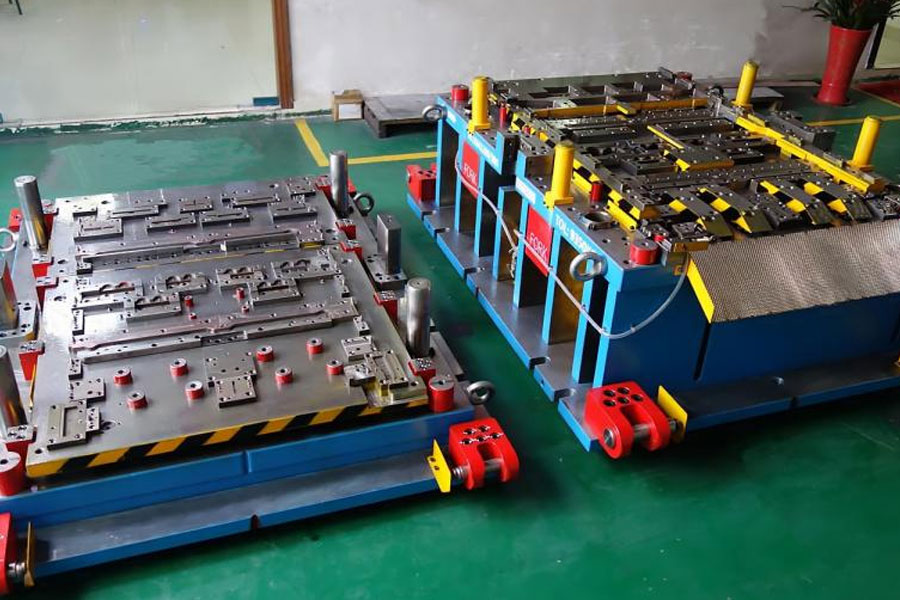
1. The lightweight of automobiles is overwhelming
Reducing the weight of the car is what people have been pursuing and exploring. Lighter cars can improve vehicle performance on the one hand, and on the other hand, it can better meet the needs of energy conservation and environmental protection. If all the steel parts of the current car are replaced by carbon fiber composite materials, the weight of the car body can be reduced by 40-50%, and the speed and steering performance of the car will be significantly improved. In addition, my country’s current motor vehicle pollutant emissions have exceeded 45 million tons. The development of lightweight automobiles is an urgent need to realize my country’s low-carbon economy. Data shows that for every 10% weight loss of a car, fuel consumption can be saved by 7%. At present, steel materials account for about 3/4 of the weight of the car body. If all the steel parts of the car are replaced by carbon fiber composite materials, the car body weight can be reduced by 300kg. The efficiency is increased by 36%, and carbon dioxide emissions can be reduced by 17%. If the weight is reduced by 20%-30%, the annual CO2 emissions of each vehicle can be reduced by 0.5T, which not only reduces the cost of use, but also becomes more environmentally friendly.
2. Carbon fiber composite materials are an inevitable choice
Carbon fiber is a fiber made of chemical fiber and petroleum through a special process. In addition to having the same characteristics of high temperature resistance, friction resistance, electrical conductivity, and heat conduction as general carbon materials, it has higher strength, light weight and more corrosion resistance. Its density is less than 1/4 of that of steel, but its tensile strength is 7-9 times that of steel, and its tensile elasticity is also higher than that of steel. It is the only substance that does not decrease in strength in a high-temperature inert environment above 2000°C. It does not dissolve or swell in organic solvents, acids and alkalis, and its corrosion resistance is outstanding. Moreover, it has a soft appearance and can be processed into various fabrics. From the perspective of use, carbon fiber does not have the problem of corrosion and rust, and it is more durable than ordinary metal. Under extreme climatic conditions, the properties of carbon fiber hardly change. The use of carbon fiber to manufacture the car body can save the costly and cumbersome painting process. No wonder some people say that carbon fiber is almost the perfect material that can reduce the weight of a car.
3. The development of carbon fiber composite technology has attracted much attention
Carbon fiber composite materials have two key technologies that have attracted the attention of OEMs. The first is modular production. Carbon fiber composite materials have good plasticity and can be processed into various parts and components, and can also be made into an integrated structure. For example, car seats need to weld 50 to 60 parts. If the whole carbon fiber composite material is used, it can be processed and formed at one time. Not only the processing time is short, the cost is reduced, and the accuracy is guaranteed. The second is the production process-the development and application of resin transfer molding (RTM) technology, which can greatly increase the molding speed of parts, shorten the traditional molding time from several days to a few minutes, and have the advantages of high efficiency, low cost, and environmental protection. Companies such as BMW, Audi, and Teijin have all tested or used this technology. The use of newer molding technology can enable carbon fiber products to meet the requirements of Class A surface, and expand the use of carbon fiber composite materials in automobiles.
Application of carbon fiber composite materials in automobiles
Therefore, under the situation that automobile lightweight has become a trend of development, the application of carbon fiber composite technology provides the best choice for automobile lightweight, and it has become an inevitable choice on the road to change. Kangde Composites is in a leading position in this field, and can provide the top carbon fiber lightweight overall solution for the development of automotive lightweight.
Link to this article : Lightweight Automotive Mold Production Is Coming
Sheet metal, Copper Milling, carbon steel,online laser cutting service, 3D printing, precision CNC machining services for heavy equipment, construction, agriculture and hydraulic industries. Suitable for plastics and rare alloys machining. It can turn parts up to 15.7 inches in diameter. Processes include swiss machining,broaching, turning, milling, boring and threading. It also provides metal polishing, painting, surface grinding and shaft straightening services. The production range(include aluminum die casting and zinc die casting) is up to 50,000 pieces. Suitable for screw, coupling, bearing, pump, gearbox housing, drum dryer and rotary feed valve applications.PTJ will strategize with you to provide the most cost-effective services to help you reach your target,Welcome to Contact us ( [email protected] ) directly for your new project.
Link to this article:Lightweight Automotive Mold Production Is Coming
Reprint Statement: If there are no special instructions, all articles on this site are original. Please indicate the source for reprinting.:Silicone And Casting,Thanks!^^