In the steelmaking process, after the converter smelting is completed, the molten steel is poured into the ladle through the converter tap;
Various alloy materials need to be added during the tapping process to achieve precise adjustment of the composition of the molten steel; the alloy materials are generally introduced from the rotating chute to the ladle when the tapping volume of the converter reaches 20%-30%, and the tapping volume Add up when it reaches 70%-80%;
During the tapping process, in order to make the alloy material melt in time and ensure the uniformity of the molten steel alloy composition, the blanking center of the rotating chute must be aligned with the molten steel injection center.
In order to achieve this goal, the current steel mill rotary chute devices adopt fixed stoppers to control the blanking position of the rotary chute body. The rotary chute device includes a rotary chute body, a shell, a rotating gear plate, a limit baffle, and a discharge Position limiter and parking position limiter, the limit baffle is fixed on the rotating gear plate, the discharge position limiter and the parking position limiter are fixed on the shell.
The electric control system and PLC control system are installed in the converter tapping operation room to realize the rotation of the rotating gear plate and drive the rotation of the rotating chute. When the limit baffle rotates from the stop position stopper position to the discharge position stopper position, it rotates The gear plate stops automatically. At this time, the blanking position of the rotating chute should be aligned with the molten steel injection center to complete the addition of alloy materials.
In the actual production process, it often happens that after the rotating chute reaches the discharge position, the blanking center and the molten steel injection center are not aligned, causing the alloy material to be unable to melt in time after being added to the ladle, and the molten steel alloy composition is uneven, and the molten steel alloy The composition hit rate is low, especially when the alloy material is added more, the unevenness of the molten steel alloy composition is particularly prominent.
2 solution
The new converter alloy material developed by Handan Iron and Steel is added to the rotating chute device, which can quickly and accurately control the position of the rotating chute blanking, and can realize the timely adjustment of the rotating chute blanking position, so that the blanking position can be automatically adjusted to the molten steel injection center. Aligned.
This kind of converter alloy material is added to the rotating chute device, which includes the rotating chute body, the shell, the rotating gear plate, the limit baffle, the discharge position limiter and the parking position limiter. The limit baffle is fixed on the rotating gear plate, The improvement is: it also includes a limiter control component fixed on the housing, the limiter control component is provided with a chute, and the discharge position limiter and the parking position limiter are installed on the limiter control component In the chute. The parking position limiter is fixed at one end of the chute of the limiter control part, and the discharge position limiter is in a sliding connection with the chute of the limiter control part.
The limiter control component is an arc-shaped plate with a chute. The curvature of the arc-shaped plate is the same as that of the shell. The width of the chute is 2-5mm greater than the width of the discharge position limiter, and the length is greater than or equal to the circle. 1/4 of the circumference of the shell.
The working process of adding this kind of converter alloy material to the rotating chute device is as follows: press the “discharge position” button before tapping, and the rotating chute body will start to rotate under the drive of the rotating sprocket. When the limit baffle on the rotating sprocket rotates When the position of the discharge position limiter is reached, the rotating gear plate automatically stops, and the blanking position center of the rotating chute body is pre-aligned with the molten steel injection center. When it is found to be misaligned, the discharge position limiter is moved Align the position in the chute; when the converter is tilted down to an inclination angle of 20%-30% of the tapping volume, press the “discharge level” button, the alloy silo will automatically open, and discharge through the rotating chute. During the process, the blanking center of the chute will always be aligned with the molten steel injection center to ensure that the alloy material falls in the impact area of the molten steel injection.
3 use effect
The device realizes the timely movement of the discharge position limiter in the chute by adding a limiter control board. When it is found that the blanking center of the rotating chute and the molten steel injection center are not in the same position and cannot be centered, the discharge position is manually adjusted. The material level limiter can ensure the centering of the blanking center of the rotating chute and the molten steel injection center, which solves the problems of slow alloy melting speed, uneven melting and large composition fluctuations during the alloy feeding process, and improves the composition of the molten steel alloy. The hit rate. The device has a simple structure and significant effects, and is suitable for popularization and application in various iron and steel enterprises.
4 Economic and social benefits
4.1 Economic benefits
1) For products produced by the new technology, the average monthly scrap steel products that avoid composition fluctuations and composition segregation are about 200 tons, 600 tons of downgraded products, the price of first-class products is 3000 yuan/ton, and the price of scrap steel is 1000 yuan/ton. After the first-class product is downgraded, the price will be reduced by 150 yuan per ton, and the average monthly loss will be reduced: 200 tons × 2,000 yuan/ton + 600 tons × 150 yuan/ton = 490,000 yuan, an annual benefit of 490,000 yuan/month × December=588 Ten thousand yuan.
2) Through the use of a new type of converter alloy material rotating chute device, the overall technological level of the converter production line has been improved. After the product quality is stable, the monthly average output will increase by 1,000 tons, creating an additional benefit of about 150 yuan per ton, and the annual social benefit: 1,000 tons / Month × December × 150 yuan / ton = 1.8 million yuan.
3) Reduce equipment consumption and maintenance costs by 29,000 yuan/month, and reduce annual costs by 29,000 yuan/month×12 months=348,000 yuan.
The total of the three items: 588+180+34.8=8.028 million yuan/year.
4.2 Social benefits
The successful application of the new converter alloy material added to the rotary chute device developed by Handan has filled the gap in the technical field of domestic converter alloy material addition method control, improved the alloy melting speed and uniformity during the alloy feeding process, and can stably improve the uniformity of the converter smelting composition Performance, thereby improving the hit rate of molten steel alloy components and increasing profitability.
Please keep the source and address of this article for reprinting: Technological Innovation to Improve the Homogeneity of Converter Smelting Composition
Minghe Die Casting Company are dedicated to manufacture and provide quality and high performance Casting Parts(metal die casting parts range mainly include Thin-Wall Die Casting,Hot Chamber Die Casting,Cold Chamber Die Casting),Round Service(Die Casting Service,Cnc Machining,Mold Making,Surface Treatment).Any custom Aluminum die casting, magnesium or Zamak/zinc die casting and other castings requirements are welcome to contact us.
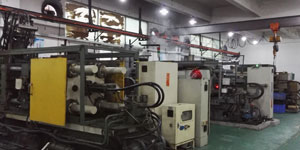
Under the control of ISO9001 and TS 16949,All processes are carried out through hundreds of advanced die casting machines, 5-axis machines, and other facilities, ranging from blasters to Ultra Sonic washing machines.Minghe not only has advanced equipment but also have professional team of experienced engineers,operators and inspectors to make the customer’s design come true.
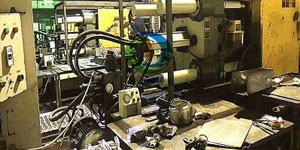
Contract manufacturer of die castings. Capabilities include cold chamber aluminum die casting parts from 0.15 lbs. to 6 lbs., quick change set up, and machining. Value-added services include polishing, vibrating, deburring, shot blasting, painting, plating, coating, assembly, and tooling. Materials worked with include alloys such as 360, 380, 383, and 413.
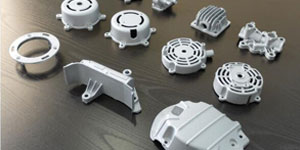
Zinc die casting design assistance/concurrent engineering services. Custom manufacturer of precision zinc die castings. Miniature castings, high pressure die castings, multi-slide mold castings, conventional mold castings, unit die and independent die castings and cavity sealed castings can be manufactured. Castings can be manufactured in lengths and widths up to 24 in. in +/-0.0005 in. tolerance.
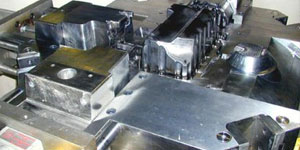
ISO 9001: 2015 certified manufacturer of die cast magnesium, Capabilities include high-pressure magnesium die casting up to 200 ton hot chamber & 3000 ton cold chamber, tooling design, polishing, molding, machining, powder & liquid painting, full QA with CMM capabilities, assembly, packaging & delivery.
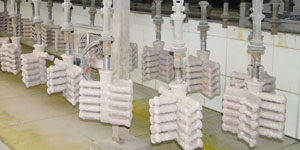
ITAF16949 certified. Additional Casting Service Include investment casting,sand casting,Gravity Casting, Lost Foam Casting,Centrifugal Casting,Vacuum Casting,Permanent Mold Casting,.Capabilities include EDI, engineering assistance, solid modeling and secondary processing.
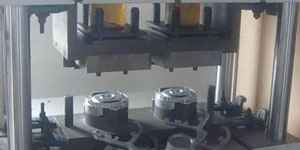
Casting Industries Parts Case Studies for: Cars, Bikes, Aircraft, Musical instruments, Watercraft, Optical devices, Sensors, Models, Electronic devices, Enclosures, Clocks, Machinery, Engines, Furniture, Jewelry, Jigs, Telecom, Lighting, Medical devices, Photographic devices, Robots, Sculptures, Sound equipment, Sporting equipment, Tooling, Toys and more.
What Can we help you do next?
∇ Go To Homepage For Die Casting China
→Casting Parts-Find out what we have done.
→Ralated Tips About Die Casting Services
By Minghe Die Casting Manufacturer |Categories: Helpful Articles |Material Tags: Aluminum Casting, Zinc Casting, Magnesium Casting, Titanium Casting, Stainless Steel Casting, Brass Casting,Bronze Casting,Casting Video,Company History,Aluminum Die Casting |Comments Off
Link to this article:Technological Innovation to Improve the Homogeneity of Converter Smelting Composition
Reprint Statement: If there are no special instructions, all articles on this site are original. Please indicate the source for reprinting.:Silicone And Casting,Thanks!^^